27 Concepts to maximize production for Robotic Assembly Automation
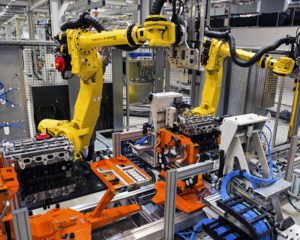
Automation carries a wide range of inherent benefits, not the least of which are an expected lower production cost per unit and a freeing up of semiskilled workers to focus on tasks that are, well, semiskilled rather than remedial and repetitive. So while the decision to automate should be an obvious one for assembly manufacturers, well-thought-out implementation is the key to a successful outcome.
Once managers have decided to automate production, they should keep several concepts in mind in multiple areas to maximize their odds of success.
Cost/Scope
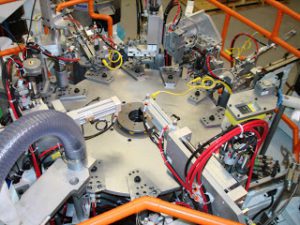
Determine the scope of the project to rein in costs. The scope includes the processes to be automated, the sequence of operations, the level of automation and control for each process, the level of material handling between each process and the target throughput rate.
Automation carries high capital costs. It is estimated that, at $4 per point of automation, raising automation from 1.0 to 10.0 costs $36 per unit of capacity.
Rather than outsourcing, employ a low-cost, incremental automation strategy that utilizes in-house resources; the latter approach is more cost-effective. Cost savings emerge in several areas. Travel expenses are reduced. A consultant does not need to sell the system, so literature and documents are simplified. Acquiring parts as needed eliminates the need to inventory large quantities of parts. In-house purchases can be made incrementally.
Identify the highest value products and future performance indicators for automation. In addition, identify opportunities for phased automation to spread out the capital cost and reduce risk.
Human capital
Evaluate the capabilities of management when considering the implementation of automation.
Even if you are a small manufacturer, don’t assume that you cannot successfully automate by putting in place a cross-functional team of employees and a flexible hands-on project management style.
Select automation “co-champions.” One will assume responsibility for design, fabrication and maintenance. The other will take responsibility for the completed system to be put into production.
Building a cross-functional engineering team whose sole responsibility is the project’s development while it is being undertaken results in increased productivity.
Assign maintenance responsibilities for the finished system to the engineering staff that designed and fabricated it. This eliminates the need for maintenance training.
Foster a culture that promotes small innovations from the entire project staff.
Determine if sufficiently skilled personnel are available for operating the assembly equipment.
Make sure that any agreements that are in place with labor unions would not restrict the movement of employees into new positions.
After system implementation, the design co-champion should focus on remaining documentation issues, spare parts procurement and maintenance procedures. The production co-champion should focus on yield numbers, throughput and operator training.
Product characteristics

Select automation products that are very stable in design and have a small number of parts or sub-assemblies for assembly line automation and design for automated assembly (DFAA).
If the time to assemble a product manually is short and the demand for the product is not high, there is little need to implement automated assembly.
Gather input from the sales and marketing team about possible future products that the business might want to automate; that input will impact the decision of whether or not to go ahead.
Assess the interface between production and packaging in the assessment. For example, if the product is backed, chilled or frozen and line shutdown would be difficult to correct with manual assembly, it would not be wise to automate the product.
Allow for product properties in relation to packaging automation. For example, the product might be sticky.
Work flow / equipment
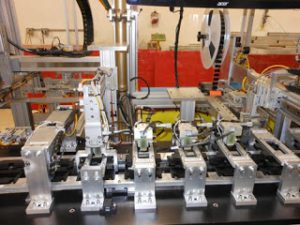
Evaluate the type of automation that will suit current operations, i.e., dedicated assembly line, Robotics, Lean automation, or the newest type using human-automation collaboration (co-robots). Assembly can require complex operations and a high task count.
To prevent the under utilization or over utilization of particular workstations that can cause bottlenecks and prevent machine overwork, implement automation services software that performs a time study of interlocked tasks and balances the workload to improve efficiency.
Build infrastructure, i.e., areas for fabricating and assembling parts, subsystems and entire machines. You’ll need a machine shop, controls fabrication area and stock room for consumables, fasteners, pneumatic components and electrical panel supplies.
Identify the potential impact of reducing of manual inspection and determine what quality control measures are necessary to replace it.
Evaluate the timing and sequence of automation implementation. Larger machines take many weeks to design and build, so allow for that in the implementation plan.
Software
If you deal with fluctuating product demand, a process configuration tool that features standard hardware and software architecture can allow you to rebalance the line.
Implementing a new line is particularly burdensome when a product launch runs over schedule. In such a scenario, the only solution is to build the line as the product is designed. Manufacturing software that allows the production line to be centrally re-configured without performing recoding can be a valuable asset.
Software that allows production stations to interlock and prevents one station from releasing a workpiece to the next one before task completion can assist in quality control.
Incorporating control software is the last major step. This software often ends up correcting many issues during debugging and testing.
References
- AllBusinessInfo.com, “Evaluate Assembly Line Automation to Properly Fit Your Manufacturing,” February 16, 2013
- Andrews, Keith: “Automation Services: Tips for Automating the Production Line,” Supply Chain Report (IDC), http://ezinearticles.com/?Automation-Services:-Tips-for-Automating-the-Production-Line&id=7498511
- Capsim Foundation, “Production,” page 4 of 5, “Automation,” http://www.capsim.com/foundation_manager_guide_2008/content/view/49/71/1/3/index.html
- Curhan, Jeff: “Automated Assembly: A Practical Guide to Low-Cost Automation,” Assembly magazine, February 22, 2011, http://www.assemblymag.com/articles/88401-automated-assembly-a-practical-guide-to-low-cost-automation
- TekPak.com, “Ten Tips for Getting Automation Ready,” August 30, 2013, http://www.tekpakautomation.com/10-tips-for-getting-automation-ready/