Robotics and Automated Assembly relieve repetitive strain injury in workers
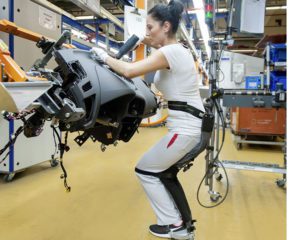
Robotics and automation offer positive benefits to workers, not the least of which is a safer, easier, and more comfortable work environment. Larger companies have a dedicated ergonomics engineer that deal with this subject while smaller ones have the automation or process engineer champion this for the company.
Low-Force Movements
On the factory floor, low-force movements such as twisting, pinching, and flexing performed repeatedly over long periods of time without rest can cause repetitive strain injury (RSI). According to the U.S. Bureau of Labor Statistics, RSIs contributed to the 476,700 nonfatal occupational injuries and illnesses which occurred in manufacturing occupations in 2015.
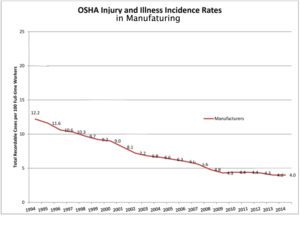
RSI can affect muscles, tendons, and nerve tissue in the shoulder, forearm, and hand, leading to pain, weakness, numbness, or impairment of motor control. RSI is a cumulative trauma disorder (CTD) related to tendinitis and work-related musculoskeletal disorders (WRMD). Work related injuries affect productivity, cost companies compensation claims and litigation expenses.
Ergonomics and occupational safety engineers try to combat CTD and WRMD with ergonomics, adjusting manufacturing workplace conditions to improve comfort, safety, and efficiency of movement. These fixes typically include, tool suspension, lift systems, hand assist tools, and adjustable work table. For work tasks with a high risk of hazard, manufacturers can boost ergonomics to another level by integrating robotics and automation technologies into factory workflows.
Adopt an approach
An approach that’s most effective in manufacturing workplaces is to leverage the ongoing improvement initiatives to accelerate ergonomics improvements. This is generically referred to as “Manufacturing Excellence,” these initiatives range from Lean Manufacturing to Six Sigma. The techniques are different but share the same common goal with bottom-line improvements by working smarter and not harder.
Human-machine hybrids
One way these technologies can relieve RSI and CTD in the workplace is with the help of robotic assistive devices. These man-machine hybrids give human workers super-human capabilities, while protecting them from injury.
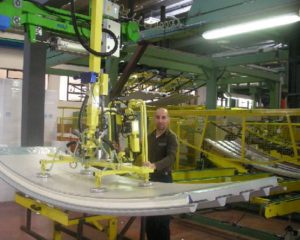
For example, intelligent assist devices (IADs) fall between traditional lifting devices and completely automated robotic solutions, it provides power assistance and motion guidance. Relying on force feedback, IADs respond quickly and smoothly to an operator’s touch. IADs enable operators to lift and maneuver naturally, as if the devices were an extension of their arms. The operator senses little or no time lapse between his actions and the system’s responses.
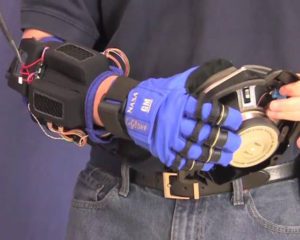
Another is a robotic glove, or “human grasp assist” designed by GM and NASA contains electro-mechanical actuators and pressure sensors which retract synthetic tendons when the operator grasps an object, and then release them when the wearer lets go. In this way, the Robo-Glove helps the operator to hold heavier objects and manipulate tools for longer periods of time. Though initially designed for a robot that will assist astronauts in space, Robo-Glove technology will eventually be used to help auto workers build cars.
Collaborative Robots
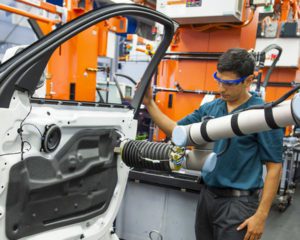
Collaborative robots make it possible for robots to operate directly with humans, thereby making them human-collaborative robots. By limiting the speed and power of the robot, the risk to humans is greatly reduced due to the energy of the collision being low enough to not cause serious injury.
Human-collaborative robots are typically used in small-volume assembly or materials handling tasks. In these applications, the robot usually handles the highly precise, repetitive tasks while the human handles the tasks that require ingenuity or manipulation.
Some advantages of human-collaborative robots are that they can work alongside people without the safety issues of industrial robots. The robots do the repetitive, tiresome tasks which reduces the rate of injury from repetitive strain.
Automated or semi-automated robotic assembly
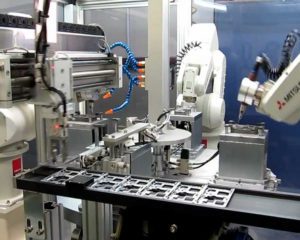
An even higher level of ergonomic protection, manufacturers turn to automated or semi-automated robotic assembly, removing the human operator completely from the hazardous task. Robots have the dexterity needed for many assembly and material handling processes, allowing human personnel to be reassigned to duties that are less likely to cause injury.
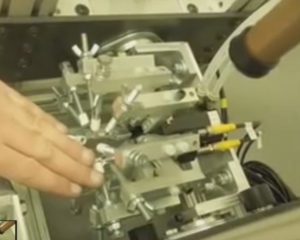
As an example, the placement of an O-ring seal on a piston , pump housing, or valve involves stretching the ring evenly over the lip of a groove for a full eight hour shift. The action can require an awkward hand position and a forceful extension of muscles and ligaments as the fingers spread open the ring. When performed repeatedly the action can cause RSI.
To mitigate this hazardous task, undergraduate researchers at Clemson University designed a robotic assembly station which uses the tooling jaws of an automated O-ring gripper to pick and stretch open a ring, and then move it into position. Once in place, a second set of jaws ejects the ring from the gripper, seating it in the groove. The researchers used an AGP-8-OR O-ring seal assembly gripper, by American Grippers Inc, to demonstrate its use in both automated and hand-assist bench-top assembly modes.
Bottom-line benefits
Using robotics and automation can mean fewer on-the-job injuries, lower insurance and medical costs, less workers’ compensation pay, and less time off of work. Fewer injuries also mean less need to hire and train new workers.
Additionally, when line workers are less tired or stressed, they get more done and have better morale. Their quality of work may also improve.
All of these cross functional ergonomic improvement factors can add up to provide a safer, more efficient—and more profitable—factory production line.
For OEM manufacturers looking to invest in robotics and automated assembly to combat RSI and CTD in their workforce, American Grippers Inc provides a complete range of sophisticated automation devices that include pneumatic and robotic grippers, rotary actuators, thrusters, linear actuator slides, mini slides, robotic tool changers, and overload devices. All products are available in imperial and metric versions for flexibility of design for a world market.
American Grippers Inc headquarters is located in Trumbull, CT, and all of our parts are made in the USA. AGI products are used in a variety of manufacturing processes, including assembly, packaging, loading and unloading, and part transfer.
To learn more concerning our assembly automation components, please contact us and we will help with your application needs.
www.prweb.com/releases/o-ring_assembly/2/prweb10468398.htm
www.dir.ca.gov/dosh/dosh_publications/EasErg2.pdf
www.bwc.ohio.gov/downloads/brochureware/publications/ManufSafeGrant.pdf
https://www.roboticsbible.com/nasa-gm-robo-glove-reduces-repetitive-stress-injuries.html
https://www.rethinkrobotics.com/blog/can-the-integrated-workforce-do-more-than-increase-efficiency/
https://www.zdnet.com/article/coming-to-a-factory-near-you-man-machine-hybrids/
https://www.researchgate.net/publication/19370396_Hand_wrist_cumulative_trauma_disorders_in_industry